Machine Calibration
The first step in process improvement
Renishaw’s laser interferometer and ballbar measurement systems assess, monitor and improve the static and dynamic performance of machine tools, co-ordinate measuring machines (CMMs) and other position-critical motion systems.
Our products should, therefore, be considered as the first step in process improvement and are complementary to the on-machine and off-machine probing systems.
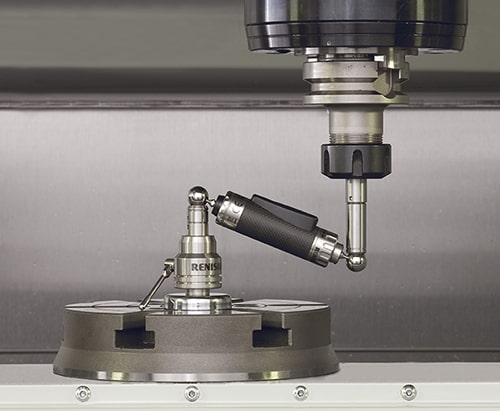
Why calibrate?
Understanding, and in some cases correcting, errors in machines, CMMs and motion systems is key to getting more value from your equipment.
Increase machine uptime
Whatever your machine or motion system, you need to know that it is up to the job before you even begin cutting, processing material or measuring components. It is important to gain a detailed picture of how each characteristic of a machine’s positioning performance is varying over time. This enables you to predict when maintenance work will be required for specific machines, and establish contingency plans in advance.
Improve machine performance
Renishaw’s performance measurement equipment allows you to manage your CNC machine tools effectively by determining a machine tool’s capabilities before machining and subsequent post-process part inspection. In addition, it can improve machine performance through targeted maintenance and error compensation.
Increase knowledge of your
machine/manufacturing capabilities
It is important to use the right machine for each job. Assigning jobs with specific tolerances to machines capable of holding these tolerances, ensures that the machine is fit for the required purpose and less likely to produce scrap.
Enable targeted maintenance
With Renishaw’s performance measurement equipment, you can clearly see what is causing the problem and if maintenance needs to be called; you have all the information to pinpoint the problem and minimise downtime.
Enable scheduled maintenance
With regular testing and comparing with older test data, you can even identify potential problems before they become critical and schedule maintenance to minimise disruption.
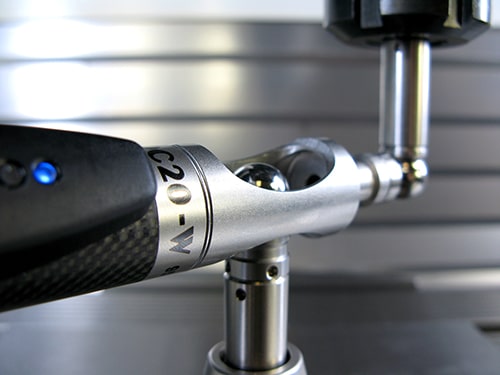
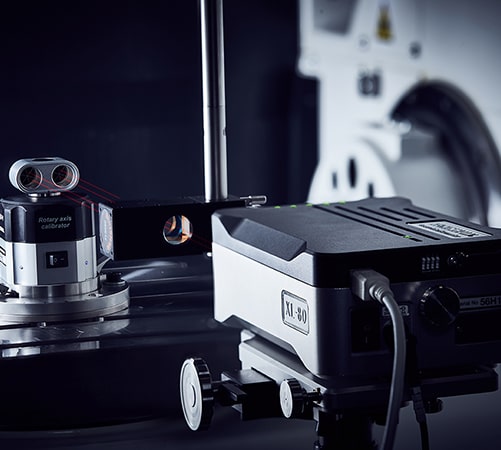
Prove the performance of your machines
When customers need confidence in the quality of your machines or process, then calibration graphs and regular performance evaluation results of your machines are excellent proof. These can give you a valuable competitive advantage over other manufacturers, who may not perform such tests.
Comply with quality assurance procedures and standards
It is a requirement of the ISO 9000 series of quality standards that manufacturing and inspection equipment is calibrated, monitored and controlled using recognized and traceable systems and methods.
Provide a professional maintenance service
High quality after-sales service is key to maintaining accuracy. Using the same calibration tools in the customer’s premises as the system Original Equipment Manufacturer (OEM) uses in their factory, is the best way to restore the machine to the original manufacturer’s specification.